Nowadays, with the improvement of material level, more and more plastic products are applying plating technology to change the material performance because of the shortcomings of easy aging, easy scratching, and easy deformation of plastic. For example, the lamp frames, faucets, and the outer frames of electrical appliances in our life look like metal from the outside, but in fact, most of them are not metal materials, they are metal materials replaced by plastic plating products.
The plated products not only look good, but also have the characteristics of metal in terms of performance. The advantages of corrosion resistance, and acid resistance, the disadvantage of expensive, if the plating quality is not good, the same will have black spots, a moldy situation.
I. Advantages of product plating
There are many kinds of plating for plastic products, and different metal materials are plated according to the usage environment to give new properties to plastic. Normal plating of plastic products is for corrosion and acid resistance to meet the needs of the product’s use. There is also a kind of plating for decorative purposes, for example, there are very many internal plastic parts in cars for decoration, not only for aesthetic purposes, but also to make them more wear-resistant and clean.
II, the principle of product plating
There are two main forms of product plating, one is water plating, the other is vacuum ion plating, because plastic is a non-conductor, if plastic parts plating, it is necessary to cover the surface of plastic products with a layer of conductive layer, plating level abs, ABS/PC is the universal plating parts of the use of materials, because in the plating of the ABS B roughening, chemical reaction can occur on the surface of the tiny pits, it can make the metal layer hang on the surface of the product. It can make the metal layer hang on the surface of the product.
III, the structure of product plating requirements
Plastic product plating is generally simple structure of small and medium-sized products, directly using the flow channel for clamping, the clamping position is 0.5 times of the main channel. Because the surface of the product is plated, no trace is allowed, so the glue is generally fed from the bottom through the slider or the slant top. And there is a column position to facilitate the stacking and placement, as shown in the picture I designed the plating products.
Red is the runner
Pink is the clamping position
Orange is the column position
Green is plating surface
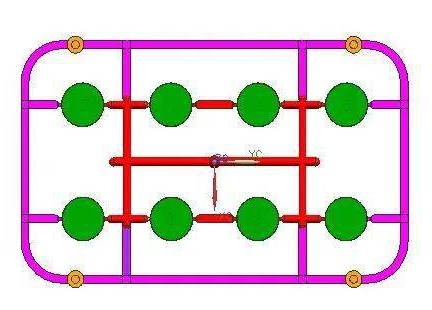
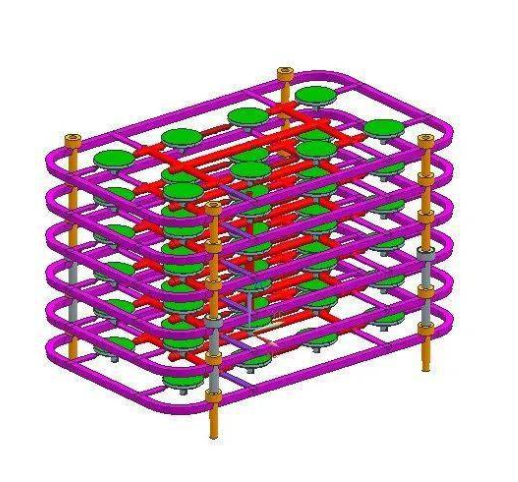
IV, product plating in the molding matters need attention
1、Molding defects
Plastic product plating is generally a simple structure of small and medium-sized products, and it is necessary to ensure that there are no molding defects when plating. If the product has defects such as shrinkage, flow marks, oversized fusion line, rupture, etc., the plated product will not only not cover the molding defects, but also magnify the defects by 1.5 times.
2、Internal stress
Plastic products in the molding process can not avoid the existence of internal stress, and when the stress of the product is too large or stress concentration, it will make the product warp and deformation or even crack. If the plastic then after plating belongs to the secondary processing, in the plating process if the plastic stress is too large will inevitably occur after the plating of the product coating fracture.
Stress relief methods.
1) The product is designed with uniform wall thickness, so that the product can shrink evenly after cooling, and try to avoid the existence of sharp corners.
2) In the mold to ensure uniform cooling of the mold water circuit, the runner diameter is too large and the length is too long will make the stress rise.
3) The ejector bar needs to be placed in the area where the material holding force is large, and the ejector speed of the molding machine is too fast, it is easy to have the problem of stress concentration, the ejector speed needs to ensure that the product is evenly ejected by the force.
4) In the process of debugging to reduce the injection pressure and speed, and improve the mold temperature, the material temperature can make the material stress reduction, shorten the injection time, and holding time are conducive to stress reduction.
5) in our production most often use heat treatment to change the problem of excessive stress in the product, the product will be placed in the 65-75 ℃ oven for 2h after the cooling to reduce internal stress.
3、Fusion splice marks
When the melt is filled, the fusion mark is made by the convergence of two or more strands of melt, which can only be reduced or changed in shape and hidden in an inconspicuous position. Therefore, when the higher the flow temperature of the melt, the greater the angle of intersection, and the strength of the fusion line will be very good.
Ways to adjust the fusion marks.
1) Increase the mold temperature and melt temperature.
2)Increase the injection pressure, and injection speed.
3) Increasing the exhaust at the end of the fusion joint, also can change the melt flow trend, so that the overflow side and the pendant side do together.
4、Surface finish
Plastic product plating requires high surface accuracy of the mold, the surface can not have scratches and burnishing treatment and trachoma, need to achieve a bright surface of the product, and also to enhance the wear resistance of the mold surface. If the surface of the mold is not smooth, it should be polished in time, otherwise, it will affect the effect of product plating.
5、Oil stain
When plating, if the product has an oil stain, it will make the plating adhesion effect not good. Before the product plating, the plating manufacturer will use an alcohol wipe, white electric oil cleaning, soaking cleaning, and other pre-treatment oil removal processes, but it is difficult to ensure that the product is no oil, so in our production time try not to use mold release agent and avoid the production of mold oil is particularly important.
6、Packaging
Electroplated products will be packaged separately during production to avoid scratches and hidden dangers for subsequent work. After plating, the plastic parts are almost the final product, and the molding processing factory will directly ship them in boxes after inspection.